Repairing the damage of a supermarket delivery van
14th century techniques used by 21st century Sarah Partridge, from community-run Orchard Barn Environmental Education Centre at Ringshall.
The old daub is the best daub
Earlier this summer, a ‘Wealden’ timber frame house in Boxford was badly damaged by a supermarket home delivery van reversing against its front elevation, causing considerable damage. The owners, Suffolk Preservation Society Members, asked if I could reinstate wattle and daub panels in their building which dates back to the 1400s. The timber frame itself was repaired by K.E. Jones & Son Limited based at Newton Green. Old daub (traditionally a sticky material usually made of a combination of wet soil, clay, sand, animal dung and straw) is always the nicest to work with because it has weathered for centuries and remixes well so I approached this task with delight.
Building with the local landscape
When people ask me what I do, I frequently tell them I build with mud and sticks. There are many things about this medieval form of construction that I love. Not least its green credentials using a coppiced woodland product that supports traditional woodland management, and the low carbon footprint of digging one’s own daub. Harvesting the sticks I visited Raydon Great Woods as I had estimated that I needed six hazel rods per panel and harvested four bundles of ten rods. The diameter varied from 1-2cm and the length needed to be as straight as I could find.
Close timber framing
Typically, our timber frame buildings in Suffolk comprise vertical wattles bound to three horizontal spars. The width of the panel varies according to the wealth of the person who had the house built and how much timber they could afford. The panels I reinstated were 30-40cm wide.
Flexibility needed
Hazel is coppiced on a seven-year rotation and it was the young and still flexible rods that I needed as I wanted to ‘spring’ them into place. I also needed 18 shorter but stouter pieces for the horizontal spars.
Instructing the builders
The builders engaged on site agreed to save all the old daub they had taken out of the wall. So instead of dumping this in a skip, as often happens, this veteran building material was salvaged for my use. Tip number one, if you ever have to disturb a vintage wattle and daub panel, always keep the daub. You can re-use every last bit of it.
Uncovering the past
Protecting my eyes and using my experience and judgement, and wishing to retain as much building material as possible, I took my lump hammer to the old daub panels and smashed it off its medieval wattle revealing remarkably well preserved sticks, possibly 600 years old. I also found ‘treasure’ in the form of historic fabric.
Lime bast as a binder
I had read about the use of Lime bast, and only this year had started to harvest Elm bast. However, I’d never seen Lime bast before, and certainly not dating back as far as this did. This was my ‘treasure’. What is bast? It’s the layer just below the bark of the tree.
Elm bast
Earlier in the year I had harvested Elm bast for a craft project. I took a draw knife and removed the bark, then with a Stanley knife scored the bast with parallel cuts about 1cm apart along the trunk of the previously felled tree. Bast is 2mm thick and when the sap is rising will peel beautifully. It looks like leather.
Demolition time
Having broken up the old panels and removed the sticks and bast (and the occasional errant lumps of concrete and hard render) I was left with the most beautiful daub complete with 600 year old straw. I damped it down and set to installing new wattle.
Creating the infrastructure
There is an art to getting the horizontal spars to stay in place with minimal intervention from modern fixings. It involves an auger hole both sides, and a chiselled groove from above one of the holes, not easy when the spacing between studs is only 30cm.
Stick management
In order to get a good fit the spar is cut over-size, inserted into the hole without the groove and then ‘encouraged’ down the groove with a maul. It was necessary to cut six sticks to length (or slightly longer than needed) and aim to wedge them into place between the sole plate and the wall plate. The pre-existing medieval shutter groove helped here as I was able to use it to hold the top of the sticks in place whilst I tied them onto the mid spar.
Modern versus traditional
I had to compromise on the choice of binding agent. I used baler twine. At least in a couple of centuries’ time it will tell the story of the evolution of the building. And yes, there is an art to getting sticks to stay still long enough to bind them in place.
Foot power
With sticks restrained in place I set about reconstituting the daub. Without the provision of cattle or horses hooves, which would have been the method, I stomped fresh straw and a little newly dug boulder clay into the damp medieval daub. It developed really well, smooth and creamy and a delight to apply to the new wattle frame.
Challenges of retrofit
‘Retrofitting’ from just one side of the wattle framing is always a challenge and I was glad I had left hand holes between the sticks – that way I could prod the daub down behind the wattle and into the external lathes. It is a slow and exacting process for the fingers and whole body.
Mark in time
All in all, it is a great ‘green gym’ activity with sound environmental credentials. Not only have I left my mark on the fabric of this lovely building but I can honestly say it was a delight to do so.
Originally published in Suffolk Preservation Society, Suffolk View.
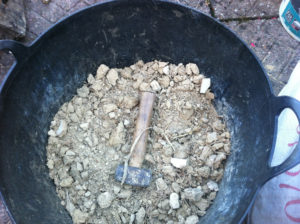
Recycling old daub
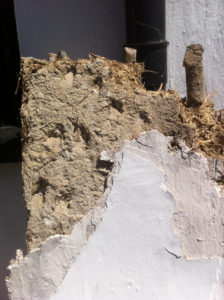
Vintage panel with fingerprints

Wattle Sticks
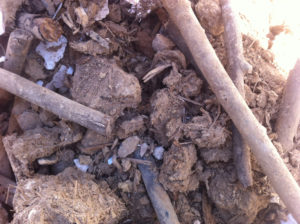
Vintage mud and sticks
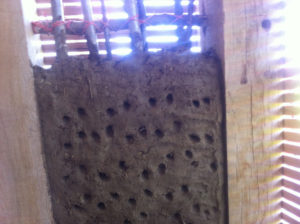
Recycled daub in new panel
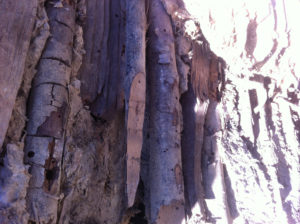
Vintage panel with lime bast binding